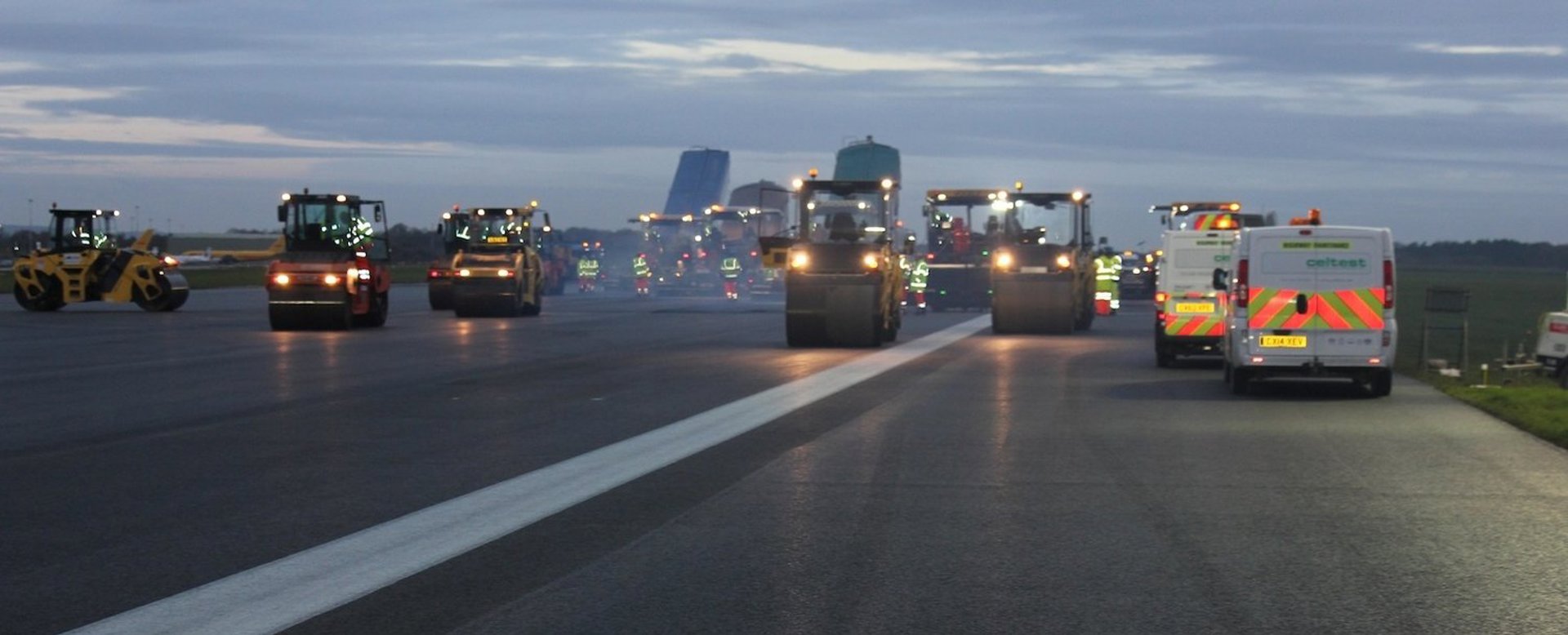
Project
East Midlands Rehabilitation Runway project
- Resurfacing works using Beton Bitumeux Aeronautique (BBA) surface and regulating courses.
- Remove existing Marshall asphalt runway surface course over a width of 44.2 metres.
- Replace with a new BBA surface course; in addition, material in the central 22m keel section was replaced to a depth of 165mm.
- Up to 800 tonnes per hour.
- 3 on-site asphalt plants producing 50,000 tonnes of coated material.
- 6 paving machines.
- 30 delivery wagons.
- UKAS-accredited mobile laboratory.
- 300 staff, including 25 Celtest staff working over 5 consecutive weekends: 36-hours continuous working.
Client
Colas was appointed by Galliford Try, which is the framework management contractor for Manchester Airport Group (MAG), to resurface East Midland Airport’s 2.9 km-long runway.
Colas delivers sustainable solutions for the design, building and maintenance of the UK’s transport infrastructure. Clients include Highways England, Local Authorities, MoD, Aviation Industry and the Private sector; contractors, consultants, architects and utility companies. Celtest has a long-standing business relationship with Colas, including work at Mount Pleasant Airport, Falkland Islands, in 2010 and 2015.
Challenge
The surfacing works were scheduled during day and night shifts across five consecutive weekends, through full-shut-downs (36 hours) of the runway.
Prior to laying the new surface, the old Marshall Asphalt had to be planed off. The new BBA surface was then laid using six paving machines, with five laying in echelon formation to ensure no cold joints were created in the surface. In addition, material in the central 22m keel section was replaced to a depth of 165mm. Three on-site mobile asphalt plants produced up to 800t/hour.
Colas has used Celtest for 30+ years, supplying expertise materials testing services on numerous airfield projects, including site lab., staff and equipment.
The East Midlands Airport project required a stringent materials testing regime. In addition to onsite training before the project started, Celtest staff received on-site inductions, with risk assessments and method statements (RAMS) devised for all elements of the project.
The project began on 5th November 2016, and Celtest operated four shifts per weekend, with day and night teams, and two supervisors. Prior to starting the project, Celtest had been involved with testing the laying trials in the compound area. At East Midlands Airport, the Celtest team mobilised a 24’ x 8’ mobile laboratory including a fully covered sample preparation area manned by three technicians.
Within the mobile laboratory compliance testing included: Flakiness Index, Particle Size Distribution, Moisture Content, Maximum Density, Binder & Grading analysis, Bulk Density, Void Characteristics, and thickness of bituminous cores.
Major challenges for the teams included working within the tight schedules demanded by the 36-hour shutdown of the runway, the cold December temperatures, and long weekend shifts from midnight Saturday to lunchtime Monday. Security was high, with MAG security clearance, ID passes, and a Radio Frequency Identification (RFID) card scanned at a manned security gate when entering/exiting the airside area.
Results
Close liaison with Celtest at the pre-contract stage ensured the client’s requirements were understood, enabling solutions to potential challenges to be planned in advance. The pre-project testing in Celtest’s mobile site laboratory ensured smooth operation after the main contract started, which proved essential to meet the stringent time constraints.
To assess performance and compliance, routine on-site tests were carried out on mixtures throughout plant mixing, during laying, and on the compacted course.
In-situ tests included: Compaction control using a pavement quality indicator (PQI); Surface accuracy using a 3-metre long beam; measurement of the Surface Macro-Texture Depth by Volumetric Patch technique; Coring; Laying records/temperature and wind monitoring.
Conclusion
This time-sensitive project was the first time a UK commercial airport had completely closed a runway over a weekend for resurfacing, and the runway was handed back to the client with comprehensive test results demonstrating full compliance with specification requirements.
The project was on time, and had zero safety incidents. Celtest has built up a unique working relationship with Colas’ company and staff, which enables progression of preliminary works at tender stage, efficient use of resources, swift resolution of any problems and completion of projections on time. Celtest is uniquely placed in the industry with its range of UKAS accreditation, and the ability to provide project resources and testing.
As David Harradine, Colas’ Technical Development Manager Airports, Infrastructure & Projects, says: “The East Midlands project has been one of the most high profile and logistically challenging contracts Colas have ever undertaken in the UK, and having everyone working together to ensure we delivered the outputs and quality required has ensured a fantastic outcome in completing in just 5 weekends.”
He added: “We are delighted with the finished product. I would like to personally thank you all for the effort and commitment that you all provided for the East Midlands project over the past five weekends. All of your staff were great lads and working the long hours over the weekends they all performed admirably.”